9 Stages In Construction Of House Plan Projects
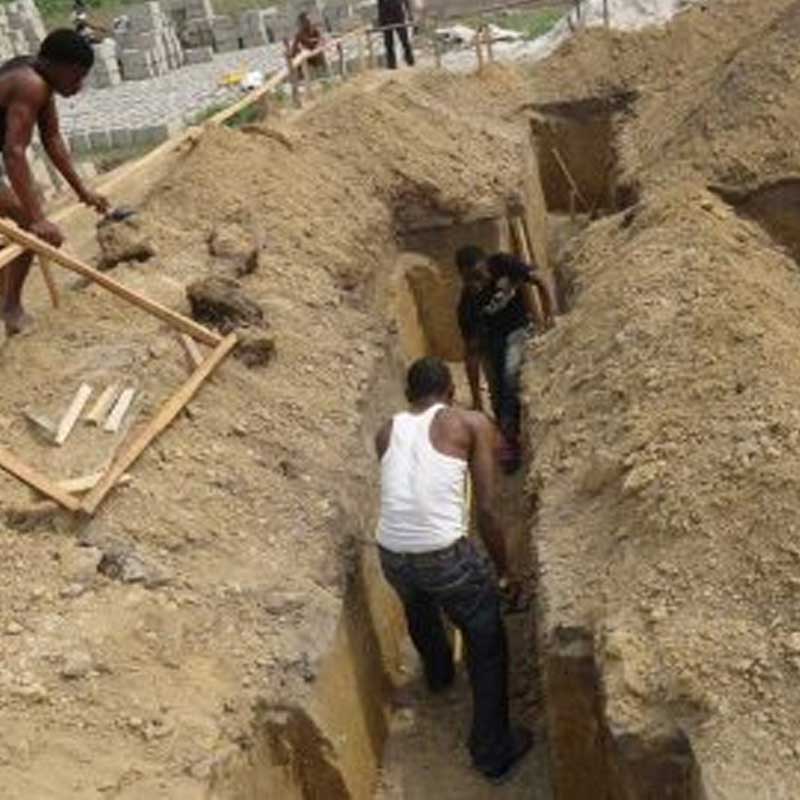
9 Stages In Construction Of House Plan Projects
Hello there, sorry for keeping waiting for this long. Last time i discuss about the Challenges And Stages Involve In House Plan Projects. if you will like to refresh your mind about it click here.
Today I will be sharing with you all the stages up to D.P.C that are involved in the construction of house plan projects.
In my previous article, I explain about leveling and blinding of foundation trenches. Once you are able to get your leveling and blinding done.
The next stage you will need to watch out for is the sub-structure stages. One way I will want to explain the sub structural work for you to understand is those construction works that are done below the natural ground floor level.
The first on my list is
1. Mounting of reinforcement basket and columns to foundation.
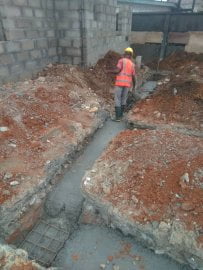
This stage requires preparation of the reinforcement to meet up with the design detailing. If you are starting a bungalow house plan you might not border yourself with this stage of work but if you intend to use concrete facial or your site location is on an unstable soil condition I will advice you introduce column at intermediate section of your house plan project to take care of structural failure.
On the other hand if your house plan is a storey building please ensure that all the house plan reinforcement is prepared to structural specification. Avoid the issue of using sub standard reinforcement. it is of my opinion that you engage the services of an engineer to guide on reinforcement detailing.
Once the reinforcement basket and columns has being prepared to detailing, make sure during placement of the basket to the column base the surface area is free from red mud. You can as well use water to flush away any sand to keep the surface clean.
One more thing during erection of the column to the basket, please make sure all the column are perpendicular to the foundation trench and inline with each other.
2. Casting of column base
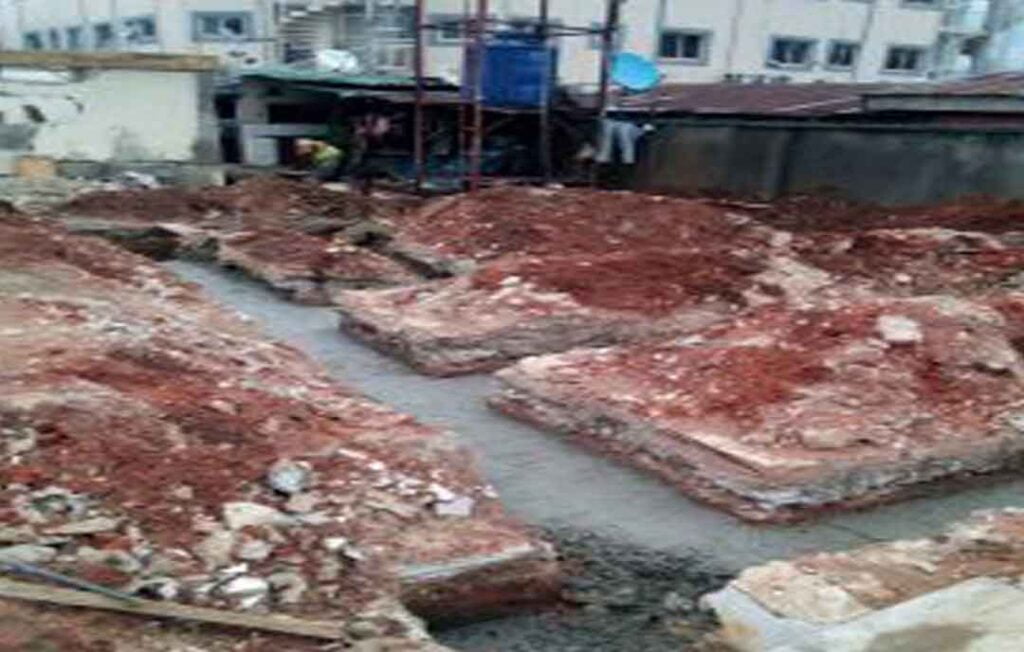
The casting of column base is the second stage after the mounting of the reinforcement basket and columns to their respective position.
This process involve the mixing of sand , cement, gravel and water in a specified concrete ratio gotten from the house plan structural details.
Care must be taking to ensure that there is adequate provision for cover to bottom and sides of reinforcement before placement of the mixed concrete to position.
During placement ensure not to pour the mix concrete from a high distance to avoid separation of materials which can lead to poor concrete strength.
3. Casting of foundation trench
Once the column base casting has being completed it is time to cast the whole foundation trench.
The thickness of concrete required for the foundation trench depends on the nature of structure for the design house plan.
The foundation trench are those excavated areas below ground level connecting the column base.
These areas need to be concrete to a particular thickness depending on the nature of the house plan structure in other to avoid differential settlement over time.
proper care should be taken to ensure that the proper mix ratio from the structural design details is adhere to and during placement of concrete the concrete should be placed at a level closer to the foundation trench to avoid displacement of coarse aggregates.
4. laying of Block work to D.P.C
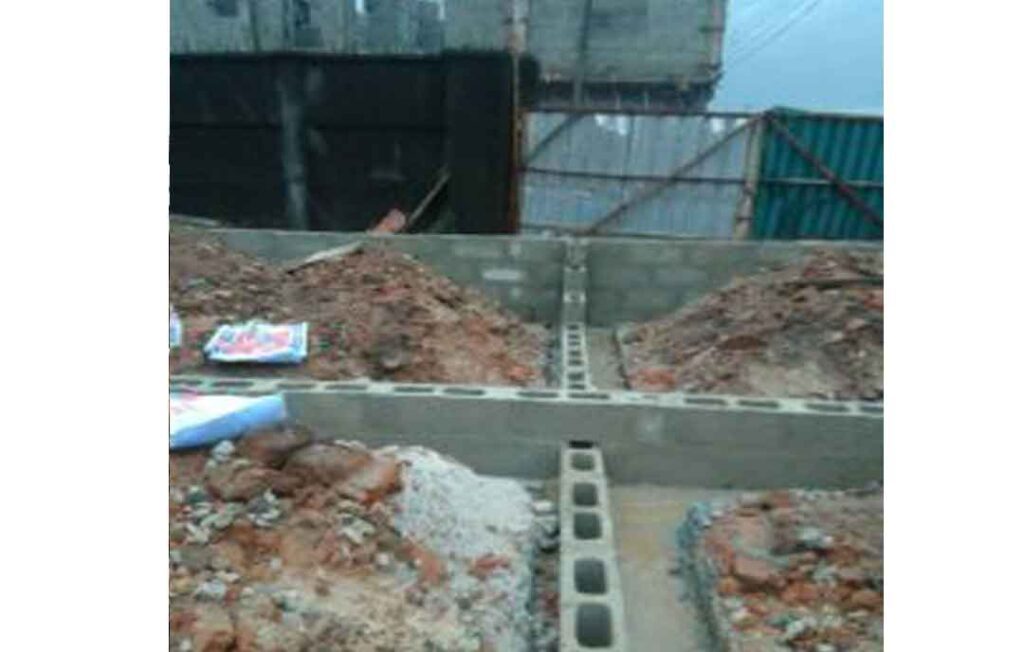
This is also know as setting out of block work on the leveled and blinded foundation trenches. it is a very important stage and of-course care should be taken to ensure all work done at this stage meets the house plan specification.
The mix ratio for mortal can be taken to be 1:4 but you can make reference to the house plan structural details to get the exact ratio. It is also advisable to ensure that both top and side of block work are at angle of 90 degree to the foundation trench.
5.Wood or panel form work to column
After taking the block work to D.P.C level. It is time to start the wood form work. You will need to look for a professional carpenter to start boarding the space between the column and the block wall.
Care must be taken to ensure that the form work are done properly to avoid wastage of concrete during casting or pouring of the mixed concrete.
There are different ways to board your columns, for economic reason i will prefer you use plywood but if you want to achieve a perfect result you can use marine boards or iron panels.
6.Casting of column
The casting or pouring process is another stage involved in house plan projects. This stage requires the mix of cement,sand, gravel and water to produce concrete which will then be pour or cast into the boarded columns.
In most cases the mix ratio to use can be found in the house plan structural design work. if your house plan project is a bungalow, i will advice you to use a nominal mix ratio of 1:2:4
The concrete should be mixed very well with good quality water that is free from impurities before casting.
The pouring of concrete should be done gentling and well vibrated in other to avoid honey comb at different areas of the columns.
it is advisable to allow the concrete to cure very well before removing the boards.
7. Filling of LITERATE sand to d.p.c
It is unfortunate most house owner do not consider this stage of work too important, simple because they want to skip the D.P.C stage thereby cutting cost.
The truth might be difficult but it will always remain valid, the consequence of not filling your house plan project is very great in the long run. it can result to dampness, cracks on the wall, differential settlements resulting to tiles deformation etc.
It is advisable to always fill your house, soak with water for proper settlement of literate before compacting it very well to make it ready for the D.P.C stage.
8. Placing of hard core to D.P.C
This stage is optional for the Nigeria system due to the high cost of hard core but if your house plan project is a structure that will be use for heavy machinery i will advice you not to skip this stage.
Placing hardcore on the well compacted literate will help to resist heavy loads on the structure which can cause damages to ground floor or D.P.C.
9. Casting of D.P.C
The D.P.C is also known or call the damp proof course in structure. It function is to provide a stable floor and stop water rising through the walls.
The casting of D.P.C requires preparation of wood form work around the edges of the house plan project to the required thickness of D.P.C
The D.P.C is an important stage in house plan project but many home owners ignore this aspect of the project for personal reasons.
Houses without D.P.C can result to structural damages relating to the ones in stage 7.
Flooring your house and fixing tiles without D.P.C will only lead to bad work at long run.
I strongly support the use of D.P.C to discourage ground water rising through the wall and causing dampness which can result to health related issues.
Once the form work is ready, casting of the D.P.C can be done by pouring the mixed concrete gradually until you arrived at the required thickness.
Ensure that the concrete is properly vibrated and the thickness level is properly followed.
This stages of house plan projects limit us to the sub structural work only.
There are others stages involved in the super structural works which will be discuss as we journey together in our later discussion on house plan projects.
Thank you for reading through this phase of article for stages involve in house plan projects, hope you find something useful about it.
You can add to to it or ask any question regarding your house plan projects through the comment box. See you on the inside for the next article on stages in house plan projects super structures.
[…] or when the surface soil is not strong enough to support the building. When embarking on any construction project, one of the most critical considerations is the […]
[…] foundation that provide effective support for load-bearing walls and linear structures. Their design and construction are straightforward, making them a practical and economical choice for many building projects. […]
Woww. That’s Nice
Great tips provided. Thanks a lot.
What is the quality of sand, stone and cement to use for blinding foundation.
You forgot to mention taking the building leveling (at 180 degree) at the D.P.C stage. What are the most reliable method available can this be done?
Is it compulsory to put in wire mesh in the DPC when building a bungalow
Hello Simon,
It is actually not compulsory in most cases but it is very compulsory in some instance, it is depending on the expected load that the DPC is about to carry.
So you need to understand the function of the DPC to know if you will design it to carry BRC WIRE MESSH or not. hope this helps.
I seriously love ur type of job and want to see more of it
I seriously love ur type of job
I found this article very interesting and educative, as a matter of fact I learnt a lot from it. I am an iron bender and my passion for construction work increases when I come across articles like this online. My question is about the mix ratio for mortal that you mentioned 1:4 got me thinking as I don’t really understand what it means. Is it 1 sand is to 2 gravel? Pls can you throw more light on this. I’d be grateful.
I think the mix ratio of mortar 1:4 means 1 head-pan of Cement to 4 head-pans of Sands
Thanks for your comment, yeah you are right. if you use head pans you are right, but not 1 bag of cement to 4 head pans of sand. okay.